La empresa El Dorado SRL concretó ayer el proyecto en el que venían trabajando desde hace tiempo, con la primera producción de ladrillos fueguinos y una primera tanda de 150 toneladas. Se trata de un emprendimiento familiar, que actualmente emplea a 9 trabajadores y prevé llegar a 20 el año próximo. Uno de los dueños, Juan Duarte, explicó las bondades de un producto hecho enteramente con material de la provincia, con el agregado de una mirada puesta en el cuidado del medio ambiente: para la combustión del horno se utilizan desechos de madera de la industria electrónica y forestal, y está previsto trabajar con energía eólica o paneles solares para la infraestructura externa. Entre las ventajas, planteó no solamente la calidad del producto sino el costo, que será similar al que se consigue en corralones de Buenos Aires, además de la disponibilidad inmediata. Esta temporada van a fabricar 50 mil ladrillos por mes y la aspiración es llegar a los 100 mil, con lo que se cubriría la demanda de la provincia.
Río Grande.- Uno de los dueños de la fábrica El Dorado SRL, Juan Duarte, dialogó con Radio Universidad 93.5 y Provincia 23 sobre la fabricación de los primeros ladrillos fueguinos, dado que ayer se hizo la primer horneada, con una producción de 150 toneladas. Explicó que “el horno es brasileño y acá se hizo el armado. Hubo adaptaciones sugeridas por nosotros para que cumpla con nuestras expectativas. Hoy tenemos el primer horno metálico móvil del país. Se usa en otros países de la región, pero en Argentina no. En el norte nuestro hay fábricas muy grandes y bien tecnificadas, y otras muy pequeñas con nada de tecnología. De porte medio prácticamente no hay y este tipo de horno responde a las necesidades de empresas de porte medio”.
“Tenemos una ventaja enorme, porque vivimos en un paraíso de descontaminación, no quemamos hidrocarburos sino desperdicios de aserraderos, aserrín, viruta, pallets molidos, desechos de la industria electrónica y forestal, y se les da una segunda vida como combustible. Tuvimos que adaptar el horno, porque era para gas. Como tenemos la voluntad de construir una empresa ecológica decidimos adaptarlo para consumo de biomasa. Hoy tenemos la asistencia de otras empresas que nos dan material, pero el objetivo es colocar una planta de procesamiento para desarmar el pallet, extraer las partes metálicas, moler la madera, secarla si hace falta, estacionarla, almacenarla y usarla como combustible. Ya estamos haciendo las pruebas y realmente funciona muy bien”, afirmó.
Destacó que este logro es fruto del esfuerzo de toda la familia. “Mi viejo está trabajando con nosotros, y ayer estaba con la pala ayudando a remover restos de arcilla para limpiar el lugar. Si bien es familiar, la empresa es ciento por ciento el corazón y la garra de mi viejo”, subrayó.
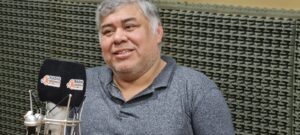
Uno de los dueños de la fábrica El Dorado SRL, Juan Duarte, dialogó con Radio Universidad 93.5 y Provincia 23 sobre la fabricación de los primeros ladrillos fueguinos, dado que ayer se hizo la primer horneada, con una producción de 150 toneladas.
Además expuso la cantidad de materia prima disponible en la provincia para proyectar una producción a muy largo plazo. “Hay arcilla para más de 500 años y esto va a abaratar los costos. Ayer comenzamos con ladrillos de cerramiento, que son de 18×33, 18×12 y vamos a hacer 18×8. Tenemos para hacer los ladrillos de techo, para hacer losas alivianadas y viñetas, y ya hicimos un pequeño lote para nosotros. Luego hay un ladrillo de vista, estructural, muy parecido al ladrillo común, pero tiene perforaciones que hacen que se trabe mejor y cumpla con las condiciones antisísmicas”, detalló.
“El nombre adecuado es bloque cerámico, más conocido como ladrillo hueco, el más grande pesa 8.8 kilos, 7.2 kilos el mediano y 6.6 kilos el más pequeño. En la primera horneada la quema se hizo en 41 horas, se alcanzaron temperaturas de 950 grados, que es la que se utiliza normalmente, y la primera producción fue de 150 toneladas. Ese es el material que entra al horno y queda un poco menos porque se va parte de la humedad”, explicó.
“El tiempo de horno fue de 41 horas esta vez y tenemos que ir ajustando de acuerdo al material de la zona y el producto, porque por ser la primera vez hicimos una receta genérica. En base a eso haremos los ajustes de temperaturas y tiempos”, apuntó.
Sin flete ni desperdicio
Comparativamente con los ladrillos que llegan en camión, habrá un ahorro de flete y de desperdicios por ladrillos que se rompen en el traslado. “Inicialmente vamos a producir ladrillos y no está previsto por ahora hacer tejas, porque hay que definir dimensiones, comprar el molde, hacer ensayos y después ubicarlas en el mercado. Los ladrillos de techo que se están haciendo alivianan la estructura en un 50% y tienen muchas ventajas, el peso para la estructura y el peso para la persona que trabaja. Además es mejor aislante de la humedad y de la temperatura, que otra una gran ventaja. Para la temporada que viene vamos a hacer un ladrillo nuevo, que en lugar de cuatro cámaras tiene siete paralelas y es termoeficiente. Es lo que se trata de implementar en provincias como Buenos Aires o Santa Fe, donde hay leyes provinciales de ahorro de energía. Todas las obras financiadas por el Estado deben tener este tipo de ladrillo. Es un poco más grande y pesado, pero es significativamente más económico a la hora de hablar de estilo de construcción”, dijo.
Precios más bajos
Consultado sobre el precio comparativo, estiman que “va a ser sustancialmente más barato a lo que se consigue ahora y comparable a los corralones del norte. No puedo dar un precio exacto porque estamos terminando de evaluar el rendimiento, los tiempos”.
La preparación
Si bien ayer se hizo visible el resultado, hubo un largo trabajo previo de montaje. “El horno tiene dos partes, una es la metálica que contiene la electricidad, la electrónica y la parte de aislación con una fibra cerámica, y la parte de las bases que es la más grande y queda bajo tierra. Hay unas 250 mil unidades que quedaron bajo una losa de hormigón bajo tierra y eso se hizo todo acá. El primer gran desafío era armar este horno, porque acá no había material, así que fabricamos nuestros propios ladrillos para el horno”, señaló.
Capacidad de producción
En cuanto a la capacidad de producción, podrían cubrir la demanda de la provincia. “Estimamos que en esta primera temporada vamos a producir unas 50 mil unidades mensuales de los ladrillos grandes. Creemos que mensualmente el mercado fueguino puede absorber 100 mil unidades, que es adonde queremos llegar. Si pudieran ser más, la planta está diseñada para producir más”, afirmó.
En cuanto a la inversión, dijo que “todavía siguen llegando equipos porque no teníamos la capacidad de comprar todo de una vez. Se compra a Brasil donde encontramos un proveedor que satisface nuestra expectativa y ha tenido un trato de primera. Llegamos a una relación de confianza que nos garantiza no solamente tener un buen equipo, sino estar bien asesorados”.
Ciento por ciento fueguino
Cabe destacar que “todo el material para la fabricación es 100% local. El ladrillo consiste básicamente en arcilla, agua, energía y trabajo, y es todo del lugar. La energía son elementos reciclables y eso nos hace diferentes, incluso el agua la obtenemos de la colección de la lluvia. Queremos que todo sea ecológicamente sustentable y la idea es que la energía externa sea alternativa, eólica o con paneles solares”, adelantó.
Personal empleado
Asimismo, valoró la generación de trabajo genuino. “Hoy tenemos netamente en la producción 9 empleados, más los integrantes de la familia, que participamos de distinta manera. Estimamos que para el año que viene tendremos 20 personas dedicadas netamente a la tarea de fabricación de ladrillos. Mi voluntad es diversificar, por ejemplo con ladrillos hexagonales, pero todo requiere de ensayos. Las tejas se usan en países con climas similares y es cuestión de demanda. Si hay demanda, se pueden hacer. Hay que adaptar equipamiento porque es una máquina estampadora que se adapta a la que tenemos”, indicó.
Aprovechamiento del vidrio
Sobre la posibilidad de aprovechar el vidrio, que no se puede sacar de la isla, informó que “hicimos una investigación y el vidrio se puede encapsular dentro de un ladrillo sin mayor problema, hasta el 20% de la masa del ladrillo, pero no le aporta valor agregado al producto. Simplemente se utilizaría como una forma de depositarlo para sacarlo del medio ambiente. Hay que preparar el vidrio, molerlo para mezclarlo con la arcilla, eso tiene un proceso y un costo”.
La segunda producción
Finalmente anticipó que “ya está en la base la segunda producción y hemos decidido dejarla para la semana que viene. Este horno tiene como ventaja que es reciclador de calor, y el calor después de la quema también se utiliza para el secado. Ahora estamos preparando el canal de distribución logístico, para la entrega puerta a puerta, y no es un dato menor. Yo me formé en la parte técnica y hay cosas que se aprenden sobre la marcha, como la comercialización, la logística, el entregar el producto al cliente en el momento que lo necesita, y sobre eso está trabajando”.
Respecto de si piensan vender en forma directa o a través de corralones, dijo que “estamos pensando en un sistema mixto. Todavía no lo tenemos definido, y también está la venta a Ushuaia. Podemos vender a clientes grandes y pequeños en Río Grande y es parte de lo que estamos evaluando. Queremos que el producto sea un beneficio para la sociedad, por la calidad del producto, por el precio más barato, y por la generación de puestos de trabajo genuinos. Nuestro padre es una inspiración, un modelo a seguir, para mi madre, para mí, para mis hermanas. Con solo conocerlo la gente se da cuenta de que es una gran persona. Es parte de la generación que nos precedió, la generación de hierro, con cultura de trabajo, y la sensación es que la que nos va a suceder es la generación de cristal, por eso tenemos que hacer algo para cambiarlo. Lo que hacen falta son ejemplos y hay que difundirlos”, concluyó.
Post your comments